-
This
was the costing for an application that was never filed, simply because
the project had no development partners and we were only notified of the
opportunity a month before the deadline.
-
-
We
have published the gist of the application to show the value returns for
potential investors - and equally importantly, to help academics
considering their own projects what might be achieved on a low budget.
-
-
For
2014, we now have Formula
E as the vehicle to drive electric car development. To this end, a
development of the LSR battery cartridge energy transfer system, is
suitable for incorporation in circuit road racers - offering pit stop
refueling in 10-15 seconds. Free developer licenses are available for
competitors. The system works equally well with batteries
and fuel cells.
-
-
-
-
Number:
29/G/ENT/CIP/12/C/N05S00 - Promotion of electric vehicle
technologies
GRANT
PROGRAMME 2012
Construction from scratch of an electric car designed for competition.
LOT
1 COSTS: ‘BLUEPLANET ECOSTAR’
Steels |
. |
1,500 |
Alloys |
. |
1,000 |
Composites |
. |
1,500 |
Paints |
. |
500 |
Wheels/tires |
2
sets |
4,800 |
Braking
& chutes |
. |
1,200 |
Glass |
. |
300 |
Suspension |
. |
2,000 |
Safety
equipment |
. |
1,000 |
Transmission |
. |
20,000 |
Motors |
. |
48,000 |
Electronics |
. |
12,000 |
Battery
cartridges |
x
3 |
120,000 |
Battery
loading mechanism |
. |
6,000 |
Solar
charging arrays |
. |
55,000 |
Welding
and other tool hire |
. |
3,000 |
Fastenings |
. |
1,500 |
Display
trailer |
. |
8,000 |
Labour:
design |
2
months |
16,000 |
Labour:
build |
4
months |
16,000 |
Labour:
electronics design |
. |
3,000 |
Labour:
web build |
. |
2,000 |
Premises
rent |
6
months |
7,200 |
Office
equipment |
. |
1,000 |
Intellectual
property: patents |
. |
5,000 |
Intellectual
property: trademarks |
. |
5,000 |
Public
relations |
. |
4,000 |
|
|
|
|
|
|
|
Sub
Total |
£
346,500 |
|
|
|
Contingency |
@
20% |
£
69,300 |
|
|
|
. |
Grand
Total |
£
415,200 |
|
|
|
CONSTRUCTION
TIMETABLE
(1)
Scheduled start-up date for the action: 15th July 2012
(2)
The duration of the construction is 4 months.
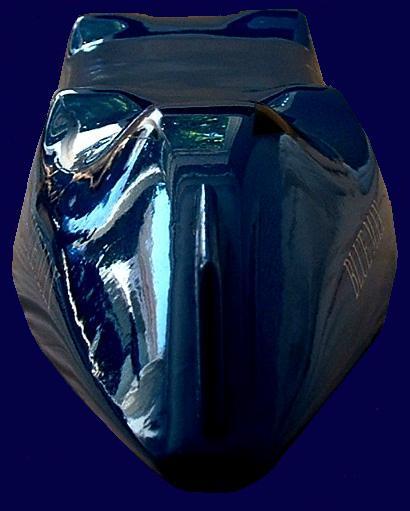
Project:
Blueplanet Ecostar
An
electric land speed record car that refuels itself by changing battery packs
between each run - charged by solar power.
Intelligent
Battery Support System
Contact us:
or phone UK:
+44
(0) 1323 831727
+44
(0) 7842 607865
Intelligent
Battery Support System
THE
BLUE BIRDS OF HAPPINESS
Enterprise
and Industry

ENERGY
GENERATING-DISTRIBUTION UTILITIES
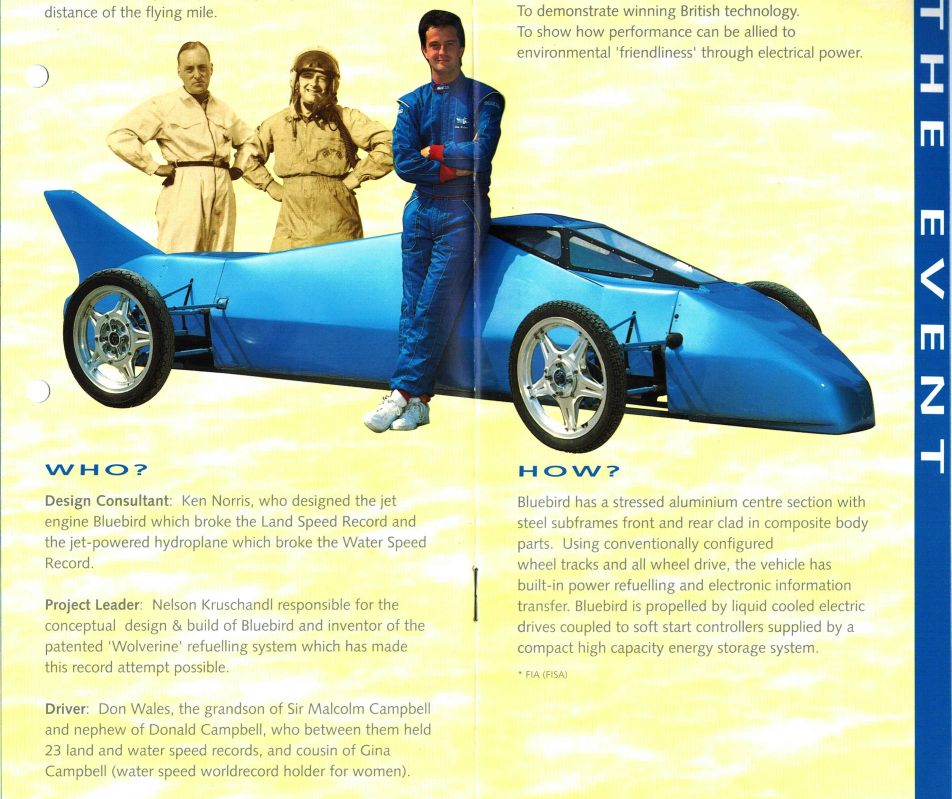
The
historic first car ever to be fitted with the patent
"self-load" cartridge exchange
energy transfer system, now under development for the FIA
Formula E racing series.
RAPID
BATTERY INTERCHANGE (RBI) An EV with RBI capability
incurs different capitalization and operating costs to an EV with a permanent battery installation.
Analysis is based upon combinations of four vehicle mission scenarios, three vehicle types, and four usage patterns.
Lead-acid battery technology is assumed in all cases as a base line for slow and fast charge batteries, and for RBI
battery modules.
The analysis attempts to reduce to an equivalent annual cost for the vehicle(s), support equipment,
electric power costs, replacement batteries, and periodic service. All vehicles and support equipment are assigned a useful
life or fifteen years, with zero salvage value.
It is
assumed that each complete slow-charge cycle to an 80% depth of charge consumes 0.2% of the life of the
battery. A fast charge cycle to a 40% charge depth consumes 1.0% of the battery life. Batteries charged by
RBI exchange equipment are slow-charged. Power costs are incurred at either off-peak rates of $0.06 per
kWh, or $0.12 per kWh for peak power (Schedule E-19 metered time-of-use service). Fast charging is assumed
to always occur during peak hours, while slow charging
and RBI module charging is assumed to occur at night, using off-peak power. Fast chargers are assumed to
have the capability of also slow-charging a battery.
Vehicular battery interchange methods have been used for over 100 years to overcome the range and charging
time limitations of EVs. Successful implementation is typically dependent upon significant infrastructure. In situations
in which necessary infrastructure is available and range demands are high, rapid battery interchange appears to
be an economical alternative to high-rate in-vehicle battery charging.
Survey results suggest that the majority of vehicle, equipment and battery manufacturers view the concept
favorably but with skepticism. Near-term feasibility is greatest for applications in which external (not owned by
the vehicle operator) infrastructure components are not required. Only fleet applications, with vehicles serviced
from a central location meet this criteria. Among fleet applications, transit buses have been and will continue
to be the favored deployment, since they operate on a fixed route with well-defined energy requirements and
periodic visits to a common location. 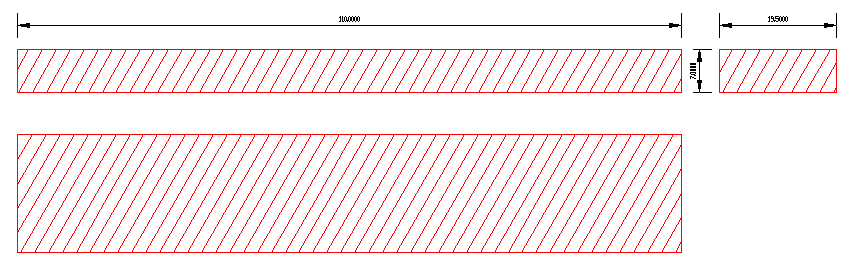
A
universal energy cartridge for sustainable future transport RBI SAFETY CONCERNS PERTINENT TO THE
VEHICLE Safety issues related to electric vehicles are significant,
but battery interchange capability does not appear to add significantly to the risk of operation compared with
conventional EVs.
Accidental release of the battery module in the event of a collision. If the battery can be exchanged quickly, it is
likely to be less securely mounted than a permanent battery installation. Accidental release of a battery
module weighing 400 to 500 kg could increase the level of damage and hazard in a collision, especially to the
other vehicle.
Battery protection from the elements, and integrity in the event of collision or rollover is also a greater concern
with an RBI vehicle, since the battery would probably be more exposed than in a fixed battery installation.
Ventilation of released gases would probably be a reduced concern with RBI, but accumulation of road
debris, mud, water and snow pose an additional problem, especially in the area of the electrical contacts.
Rain or slush laden with road salt is an effective conductor, capable of shorting and/or
degrading battery and instrumentation contacts.
Electrical connectors that must engage automatically and quickly in an RBI vehicle are likely to be more
susceptible to poor contact or accidental short due to misalignment or mishandling. The contactor system
must be completely “idiot-proof,” capable of withstanding backward insertion of the battery module, poor vehicle
alignment, and possibly excessive vehicle speed upon docking with the battery exchange equipment.
CONCLUSIONS Where
fast charging is used, not only is the battery degraded more quickly, but the
electricity consumed is charged at a higher rate. On this basis and as EVs
become popular once again, RBI is a must. Not only that, RBI allows an
operator to upgrade battery or fuel cell technology without modification to
his vehicles. Extracted
from a study by: C. Arthur MacCarley
California Polytechnic State University, San Luis Obispo,
California, USA
|