HULL
COATINGS PTFE
and silicone coatings are said to offer some performance enhancement short term.
Inert precious metal (gold, platinum) or cuprous-nickel plated hulls have yet to
be evaluated as a possible coating that prevents marine growth, and/or as an electrode
for electrolytic generation of micro bubbles. Galleons of old were sheathed in
copper plate to prevent marine growth from slowing the ship, so plating is
nothing new. INTERNATIONAL
PAINT - Two New Anti-fouling Coatings Introduced - Friday, March 01,
2013
International Paint introduce Intercept®8000 LPP & Intersleek®1100SR a biocide-free slime release coating. International Paint, part of AkzoNobel, the world’s largest global paints and coatings company, announced
at a press conference at London’s IET by the Thames, a sea-change in hull performance with the launch of two new coatings solutions.
The new products are, firstly, Intercept 8000 LPP, a biocidal linear polishing polymer antifouling featuring patented ‘Lubyon’ technology intended to deliver predictable long term performance for in-service periods up to 90 months. And secondly, Intersleek 1100SR, said to be the first biocide free fouling control coating featuring patented slime release technology to combat micro fouling on ships hulls, maintaining performance throughout the docking cycle, again offering 60- to 90-month in-service periods.
The Lubyon polymer technology of Intercept 8000 LPP is claimed to offer consistent and predictable linear polishing, replicating the effects of the banned tributyl tin (TBT), which the company says will enable ship operators to plan and budget effectively throughout the dry-dock cycle of the vessel.
The technology provides a ‘superhydrophilic’ surface, meaning that when the coating is immersed, the polymer reacts with seawater via a constant surface active zone, which offers both a lubricating effect, resulting in less friction, and releases the optimum amount of biocide over the scheme life to control fouling settlement. Reduced friction means less drag, representing likely savings in fuel and of 5% annually compared to typical controlled-depletion polymer antifoulings. The coating surface swells on contact with seawater, helping to smooth out imperfections and potentially further reducing drag. Critically, the release rate of the copper-based biocide is largely unaffected by seawater temperature thanks to the Lubyon polymer, giving further control and consistency. 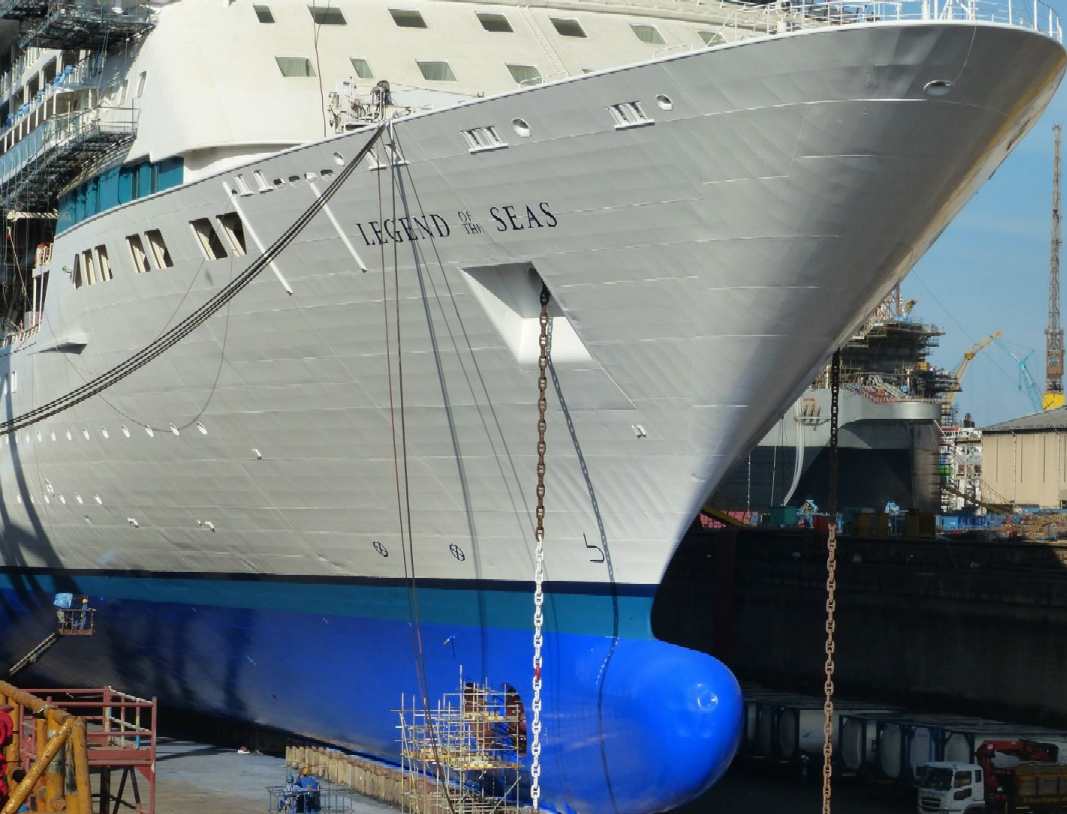
Unlike typical silyl and metal acrylate antifoulings, the polishing rate of Intercept 8000 LPP remains constant throughout the in-service period, replicates the linear polishing of the benchmark TBT-based coatings. The coating has undergone extensive trials on various ship types including container ships, tankers, bulk carriers and LNG carriers.
For owners not able to make the initial investment in the premium Intercept 8000 LPP product, a lower-cost mid-range version has been introduced, known as Intercept 7000, which offers the linear polishing of Lubyon technology, but not some of the other advantages such as temperature consistency and low drag.
At the same time, International has launched Intersleek 1100SR, to tackles the market’s ‘slime challenge’. According to the company slime is a complex, varied and dynamic organism which begins to colonise surfaces as soon as they enter the water, and which has been proven to have an adverse effect on efficiency, resulting in a decrease in fuel economy and extra emissions.
Designed to be effective even at slow ship speeds, Intersleek 1100SR is claimed to deliver outstanding macro- and micro-fouling control with good static resistance even in warm waters, making it particularly suitable for slow steaming. Any slime built up during static periods is released once the ship moves, thanks to the patented fluoropolymer which enhances the slime resistant polymer groups used in earlier generations of
Intersleek.
International says it has undertaken comprehensive research into slime growth, including a three-year fundamental research programme involving marine biologists, hydrodynamicists and polymer scientists, supported by independent academic institutes. Testing has been carried out over four years of laboratory trials backed by in-service trials undertaken with several major ship operators.
Designed to address the industry issues of predictability in antifouling performance not seen since the days of tributyltin and the difficult issue of slime fouling on ships hulls, the two new technologies are set to improve vessel operating performance, increase efficiency and help control fuel costs and emissions.
• Intercept®8000 LPP, is a brand new biocidal linear polishing polymer antifouling featuring patented ‘LUBYON®’ technology that delivers predictable long term performance for in-service periods up to 90 months, and;
• Intersleek®1100SR, is the industry’s first biocide free fouling control coating featuring unique patented slime release technology that combats micro fouling on ships hulls, maintaining performance throughout the docking cycle .

Intercept®8000 LPP
The unique LUBYON® polymer technology gives the coating a ‘superhydrophilic’ surface. When the coating is immersed, the seawater has a lubricating effect, resulting in less friction. This reduces drag and increases vessel efficiency giving average fuel consumption and associated emissions savings of 5% annually compared to typical controlled depletion polymer antifoulings. The coating surface also swells on contact with seawater, helping to smooth out imperfections and potentially further reducing drag.
Designed for the deep sea market at newbuilding and maintenance and repair, the coating has been extensively monitored with in service performance validated on multiple vessel types including containers, tankers, bulk carriers and LNGs representing over 4 million dwt.
Intersleek®1100SR
The shipping industry’s first biocide free, fluoropolymer technology coating technology that tackles the market’s age-old ‘slime challenge’. Slime, a complex, varied and dynamic organism which begins to colonise surfaces as soon as they enter the water, has been proven to have an adverse effect on the efficiency of all vessel types.
According to a recent formula produced by Michael P. Schultz, Professor, Department of
Naval Architecture & Ocean Engineering, US Naval Academy, at today’s
bunker prices, the effects of slime potentially costs the shipping industry 44 million extra tonnes of bunker fuel, $28.6 billion in additional fuel costs and an extra 134 million tonnes of
CO2 emissions every year.
Designed for all commercial vessels, even when slow or ultra slow steaming, new Intersleek®1100SR slime release technology delivers outstanding macro and micro fouling control with good static resistance even in warm waters.
http://www.marinelink.com/news/antifouling-introduced352106.aspx

KISS-COTE
v PTFE
Self-Bonding Polymers (KSBP*)
are claimed to provide a non-stick drag-reducing finish so boats will go faster on less fuel.
Conventional marine coatings have two principal mechanisms of action. The anti-fouling character is from soluble heavy metal salts which poison the marine life that grow on the surface. This is combined with a "self-polishing" or "ablative" character. The toxins are held in a slowly dissolving matrix which has two purposes:
1. Its continuous loss of surface layer allows exposure of fresh toxins as the toxins at the surface become depleted;
2. Marine organisms will still grow on the surface despite the presence of toxins, so the coating also "sheds" it surface layer, shedding the marine growth with the eroding surface.
The majority of KISS-COTE formulations are "fouling-release" because of their inert non-stick finish. Since they are non-toxic they are not anti-fouling. However, marine organisms do have trouble colonizing KISS-COTE treated surfaces since they need an adherence mechanism to colonize. As an example,
it is claimed that Zebra Mussels will selectively colonize any other surface, including Teflon® (PTFE), rather than growing on KISS-COTE.
Products containing PTFE as the active ingredient are not anti-fouling. However, some anti-fouling coatings are available with low levels of PTFE, the most common being VC-17 by Courtalds. Please note that barnacles will grow on and penetrate a PTFE coating and Zebra Mussels readily colonize PTFE. Barnacles do not stick to or penetrate KISS-COTE and Zebra Mussels avoid substrates coated with
this material.
KISS-COTE's MegaGuard Marine LiquiCote combines the benefits of KISS-COTE Polymers with the anti-fouling effect of conventional bottom paints. The LiquiCote is applied simply by painting over a standard anti-fouling
paint, softening the surface layer of the bottom paint. It dries in a few minutes, with the bottom-paint re-hardening into a non-stick anti-fouling finish that exhibits reduced drag. The life-expectancy of the anti- fouling and the non-stick character is determined by the quality of the bottom paint. We are finding a 9-12 month life in our harsh salt-water environment. At the end of this time, one is left with a conventional bottom-paint that can easily be pressure washed and re-coated with the LiquiCote. Meanwhile, the bottom paint lasts years longer and does not leach the same high levels of toxic biocides into the water. In addition, there is much less contamination than one would find using a standard maintenance protocol on a regular bottom paint, including frequent sanding and re-painting.
(KISS-COTE, KSBP and
MegaGuard are trademarks of KISS Polymers LLC. US Patent #4,839,456. Copyright 1993, KISS Polymers LLC. all rights reserved.) The
SolarNavigator team hope to be able to run tests on as many of the above and
report those findings in the years ahead. Meantime, a patent is in progress
concerning a formula for zero
pollution craft.
LINKS Connect
innovateuk vessel efficiency competition http://www.kisspolymers.com/Products/marine.htm
|